A numerical analysis of unsteady transport phenomena in a Direct Internal Reforming Solid Oxide Fuel Cell
Growing popularity and rapid development of Solid Oxide Fuel Cells (SOFCs) stem for their potential to become a gamechanger in the field of clean power generation technologies.
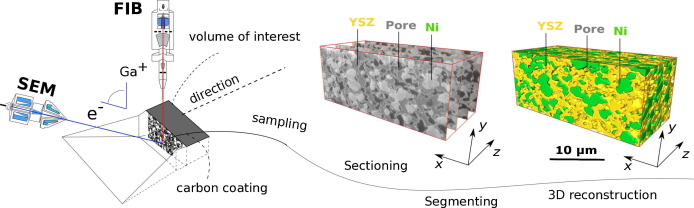
In this paper, a transient microstructure-oriented numerical simulation of a planar Direct Internal Reforming Solid Oxide Fuel Cell (DIR-SOFC) is delivered. The performance criteria in a direct steam reforming for a fuel starvation scenario are analyzed in order to optimize the underlying process. The proposed two-dimensional multiscale model takes into account mass and heat transport, electrochemistry, as well as the intrinsic steam-reforming kinetics. In the paper, the methane/steam reforming process over the Ni/YSZ catalyst is experimentally investigated to verify the used chemical reaction model. A threedimensional digital microstructure representation of the commercial anode is analyzed using a Focused Ion Beam-Scanning Electron Microscope (FIB-SEM) and the nickel-pore contact surface is calculated to relate the reforming reaction rate to the catalyst’s active area. Based on the complete DIR-SOFC model, a parametric study is carried out, to simulate the dynamic response of a fuel cell for different design and operating conditions. The results prove the dominant impact of inlet fluid temperature and methane content on the calculated distribution of hydrogen across the channel, while the collected current density was found to be a less important factor. The simulations indicate, that in the case of the direct reforming, fuel starvation is likely to occur in the upstream of the anode channel, where the reforming reaction does not keep up with producing hydrogen. The obtained results provide a significant insight into safe and efficient control strategies for Solid Oxide Fuel Cells